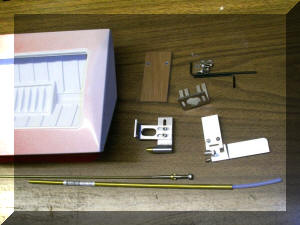 |
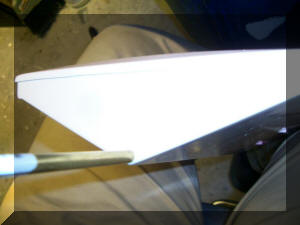 |
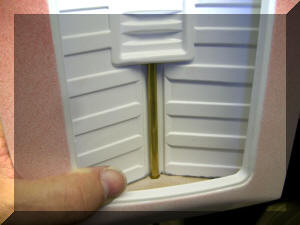 |
Hughey-type flex drive and strut with a
95mm aluminum rudder. |
Hole in the transom for the brass tube
is at the bottom of the hull liner. |
Test fit of the brass tube. Make sure it
can sit straight without any binding. |
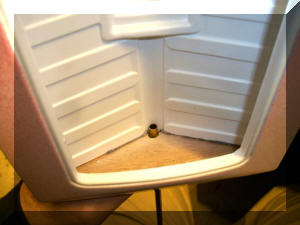 |
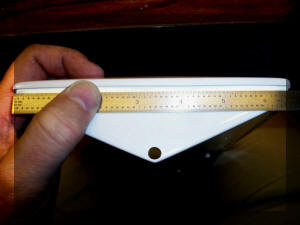 |
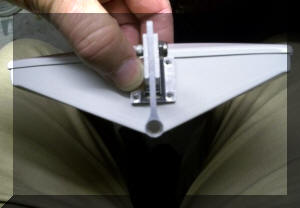 |
The hole does not have to be perfect.
Sand this area where you will be applying epoxy later. Sand the rear
2/3rds of the motor recess as well. Don't forget the inner sides of the
recess. |
Find and mark the center of the transom. |
Center the strut, you can loosen the
lower strut and align it to the shaft hole to be sure of a good fit &
alignment. |
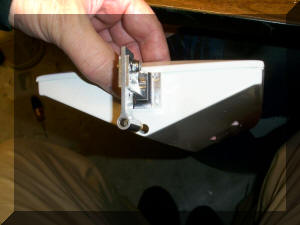 |
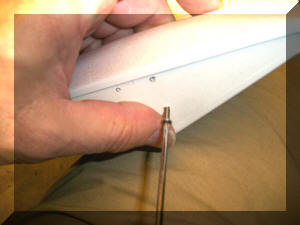 |
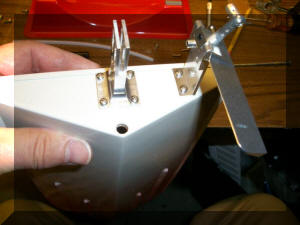 |
Hold the strut with bracket in place and
mark the 4 mounting holes. |
Drill with the size bit needed for the
screws that come with the purchased drive. |
Install the rudder on the right, as far
as it will go, centered under the deck lip, and above the bottom of the
hull as shown. |
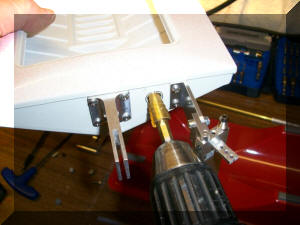 |
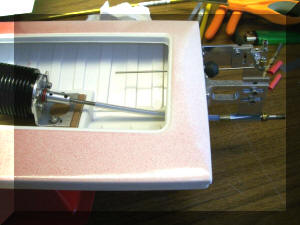 |
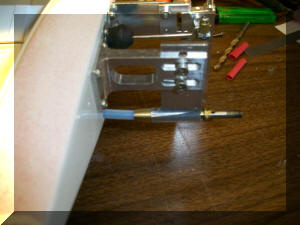 |
Locate the hole for your rudder pushrod
and use a step drill to make the large hole, or start with small drill
sizes and work your way up. |
With just the silicone rubber liner
around the flex shaft, set the motor and shaft in place. You will have
to cut the flex shaft to length. Here a straight 1/8" coupling is used
with a 1/8" thrust bearing. A self-centering collet-type coupling is
best. |
Note the gap between the strut and the
prop drive-dog. You want the prop thrust to be borne by the motor thrust
bearing, not the drive dog against the strut housing. |
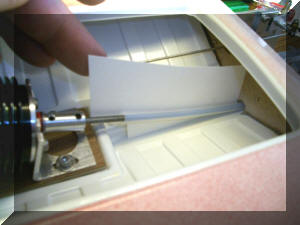 |
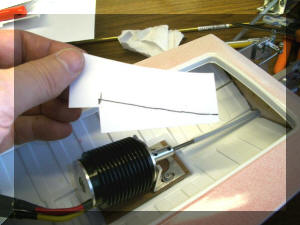 |
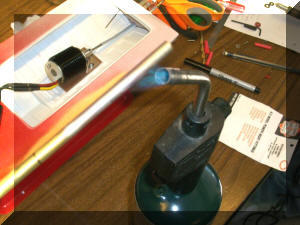 |
The shaft and liner will flex naturally.
Use a scrap of cardstock to mark that curve. |
Curve of the shaft between the transom
and the motor. |
You can bend brass tube after it is
heated cherry red, then quenched in water. Don't burn yourself.... |
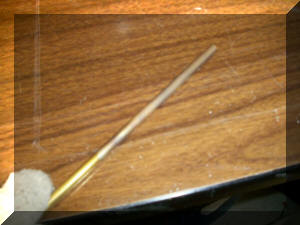 |
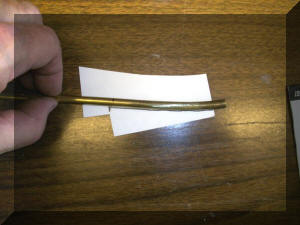 |
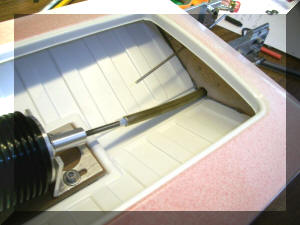 |
The tube has been "annealed" by the
previous process. |
Carefully bend the soft tube to match
the curve on your card. |
Install the tube without only about 1/8"
sticking out of the transom. Check for a non-binding fit. Here the motor
and base are sitting at the rear-most position of the motor recess in
the hull liner. |
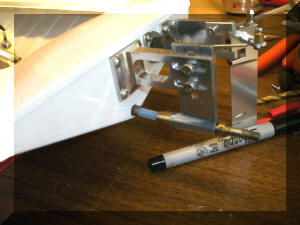 |
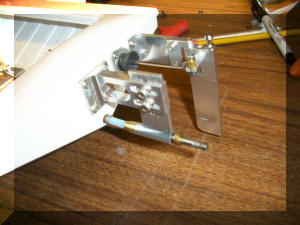 |
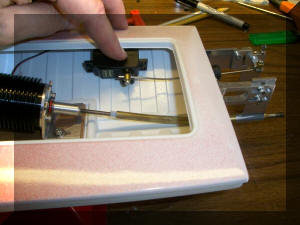 |
The outside should look like this. |
Install the rudder pushrod. Look at the
"Straight Drive Installation" page to see how to CENTER your servo and
trim the servo arm. |
Locate the right spot for the servo so
there is no binding and the pushrod is in the center of the hole in the
transom. Mark this spot and sand the floor of the spot so the epoxy will
stick properly. Score the motor tray recess as well. |
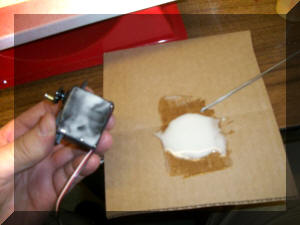 |
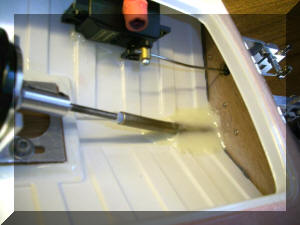 |
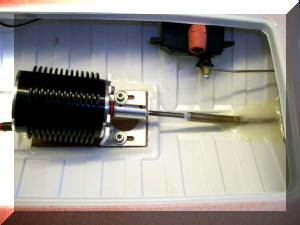 |
Carefully score the bottom of the servo
in 4 directions with a hobby knife and coarse sandpaper so the epoxy
will stick to it. Mix 30 minute (2-ton Devcon) with filler (talcum
powder used here.) and apply to the servo. Apply filled epoxy to the
base of the motor and the hull recess as well. |
Apply filled epoxy to the servo and to
the stern tube. Here, I used an eraser to help hold the servo in place.
Tape will also work well. |
Set the motor into the recess. Add epoxy
around the edges of the recess to help hold the motor in place. Set the
boat on a folded towel or use the boat stand at an angle to keep the
epoxy from running away before it cures. |
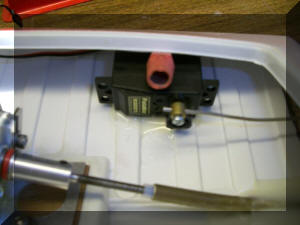 |
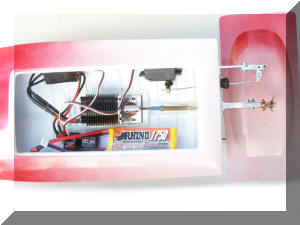 |
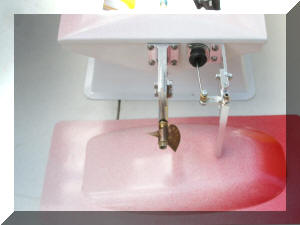 |
Check to see that the rudder works
without binding and that it doesn't slide out of position before the
epoxy sets. |
Typical finished installation.
|
Stern.
|
|
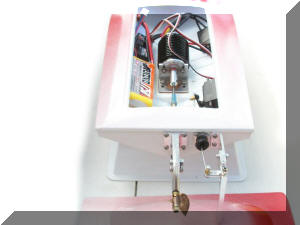 |
|
|
The battery can be moved around to
adjust the center of gravity of the boat. Support the boat with one
finger at the bow, and the second at the rear of the hatch opening
centered on the rudder. Lift the boat to check for left-right balance. |
|